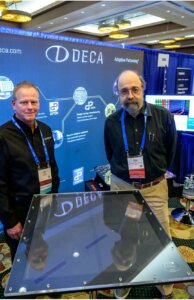
One of the most popular booths at the recent IMAPS DPC was that of wafer-level fan-out technology provider, Deca. Their black tee shirts state “SHIFT HAPPENS” on the front and on the back say, “We clean it up” (referring to their adaptive patterning of course). Also of great interest was its panel processing show-and-tell (figure 1).
At the IMAPS Device Packaging Conference, Deca and ASE jointly presented “High-Density Fan-out Chip on Substrate using M-Series and Adaptive Patterning Technology.”
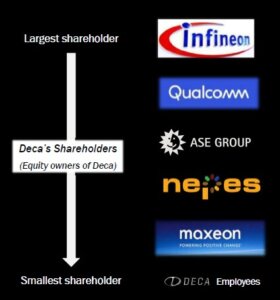
DECA claims to provide the industry’s #1 fan-out technology with 3.5MM devices shipping per day in 1Q 2022. DECA ownership is shown in Figure 2. Its technology is currently licensed by ASE, Nepes (Korea), and Skywater. More than 2.5B M-Series devices have been shipped by DECA licensees. ASE is scaling up a 600mm panel line in Taiwan, and Skywater has announced it will be building a 200mm line in Florida.
Deca believes its ultra-high density organic solutions are positioned to replace silicon interposers.
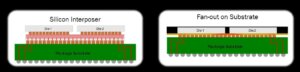
IFTLE’s previous discussions on Deca’s wafer-level fan-0ut technology can be found in:
- IFTLE 489: “AMAT Addresses Hybrid Bonding; DECA M-Series Continues to Develop”
- IFTLE 425: “Deca FOWLP is Going Mainstream; Highlights from Hot Chips
The company claims its Gen 1 technology is currently on par, density-wise, with Intel EMIB technology and TSMC InFO-R (Figure 4). Deca is presently moving to its Gen 2 M-Series technology and claims it will provide a 5X density increase.
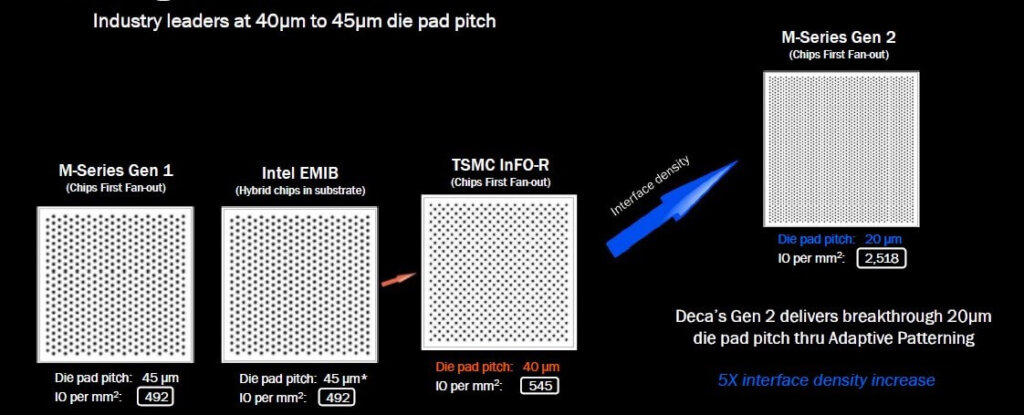
This is done by eliminating the capture pad layer through the use of adaptive patterning.

The technology also eliminates reticle size limitations (usually 850mm sq) by using maskless laser direct imaging (LDI) lithography systems.
A second Deca presentation entitled “Mask-less Laser Direct Imaging and Adaptive Patterning for Fan-out Heterogeneous Integration” discussed the details of LDI imaging and adaptive patterning.
The LDI tool is adapted from Hitachi Via Mechanics (now Adtec Eng) and features the following:
- There is no photomask with LDI – 100% laser exposure from GDSII file
- No reticle limitations to module size (without stitching)
- Supports 200, 300 and 600mm formats
- Laser beam is guided over the wafer or panel with spot sizes < 3.5µm and throughput of 55 to 110 wph for 300mm.
- Data resolution is currently 1µm on Gen 1 tool moving to 250nm on Gen 2 tool
Deca reports that it drove several custom enhancements to the original PCB platform including:
- enhanced optics, spot size reduction
- expand exposure area to support 300mm and 600mm formats
- vision system upgrades
- integrated wafer handler and pre aligner
- enhanced temp control
- ceramic chuck for tighter overlay and CD control
- data transfer enhancements
- new software for GDSII data management (vs Gerber)
One of the key challenges has been the selection of proper resists and dielectrics since LDI photolithography uses 405nm output source.
The lamination process for dry film resists requires robust equipment design and process control to ensure 100% void-free lamination. Advanced dry films now use vacuum lamination (vs roller lamination) to avoid concern for the sensitive device structures underneath the film.
For all the latest on Advanced Packaging stay linked to IFTLE…………………….
Editor’s Note: Be sure to stop by and visit the Deca Booth at IMAPS Advanced SiP Conference, June 21-23 in Sonoma, CA.