Since TSMC made its announcement late in 2020 that they were potentially building a semiconductor fab in Arizona, the reshoring movement has built up steam. Add in the current mess of supply chain issues and shortages that have been created by the pandemic, the USA’s tech trade relationship with China, poor inventory management, and Intel’s inability to manufacture 7nm chips when they said they were going to, and you get a head of steam that could make a boiler explode. In an industry that is known for looking ahead both in technology and manufacturing, how is it that both Europe and the United States let chip development technology, and chip manufacting slip away? The simple answer is economics and profitability.
In the 1990s US and Europe were at the top of the semiconductor supply chain. Table 1 table shows semiconductor sales from 1985-2011 and shows the geographic shift in business.
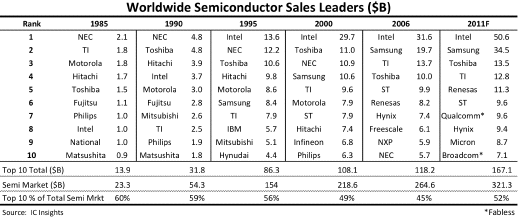
In 1985 through the mid-1990s memory was king; even Intel made memory chips. Memory drove technology and more importantly, lithography. Nikon was the lithography leader due to better optics and cornering the majority of the Japanese and then the Korean memory markets. The company eliminated US stepper competition and was able to outpace Canon.
Memory Moves Offshore
During the 1980s the memory market shifted to Japan, and then in the 1990s to Korea.
In an attempt to maintain some form of control, American semiconductor companies partnered with or licensed technology overseas. I remember in the 1990s walking into a Korean fab only to meet some former co-workers working with a Korean company to transfer technology. Most American companies continued to manufacture or partner in memory through the mid to late 1990s, before exiting or selling the business consolidating the industry. As mentioned above, memory drove process technology, more importantly, stepper or linewidth technology, so one needed a position in DRAM to stay competitive from a technology perspective until logic became the key driver in the late 90s early 00s.
The Asian companies also had a stronger focus on quality and were able to manufacture chips at a lower cost. This was in part due to salaries, and assistance from the governments in tax holidays or land at a favorable cost. In many cases, this is still the case for companies locating fabs overseas. The US exported quality control in the form of Juran and Demming statistical methodologies, only to re-import once the success of spending time on quality control became evident. As a result of not being able to compete on cost or quality, America’s and Europe’s memory businesses shrank and, except for Micron, the bulk of the industries DRAM and NAND are manufactured overseas. China has been making a strong effort in the DRAM and NAND business, with limited success as Samsung, Hynix, and Micron have approximately a 94% market share in DRAM, and each work hard to maintain that share. However, a significant portion of Micron’s manufacturing is overseas, enabling them to compete on pricing with Hynix and Samsung.
The Emergence of Foundries
Jerry Sanders once said “real men own fabs”; However, that was before technology and manufacturing became a high-stakes arm’s race. Today only TSMC, Samsung, and Intel have state-of-the-art logic fabs. Add Hynix and Micron to that mix and you round out the top five semiconductor manufacturers worldwide. Capacity is added as it is either anticipated or contracted. Adding capacity, especially building a new state-of-the-art fab costs at least $10 billion today and typically more and typically takes two years before significant product-starts shipping.
Semiconductor foundries started in the 1980s when ITRI spun out UMC. TSMC started in 1987 and you could say that the rest is history. When foundries started up, they were two to three generations behind the leading edge and would run legacy parts for the IDMs and startups emerging, such as Xilinx and Altera.
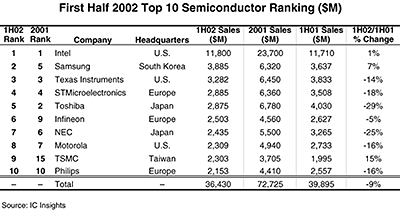
The foundries drove the fab-lite and then the fabless industry as TSMC and Samsung were able to start competing at the leading edge. TSMC cracked the top 10 in semiconductor rankings in 2002 (table 2) and never looked back. Instead of building new fabs, US and European companies would leverage foundry capacity. Motorola/Freescale, AMD, and TI, were just a few of the US manufacture to leverage foundries as the economics favored using a foundry model rather than building a fab that may only see 50% utilization. There is another industry saying: Happiness is a fully loaded fab.
Fast-forward to Today
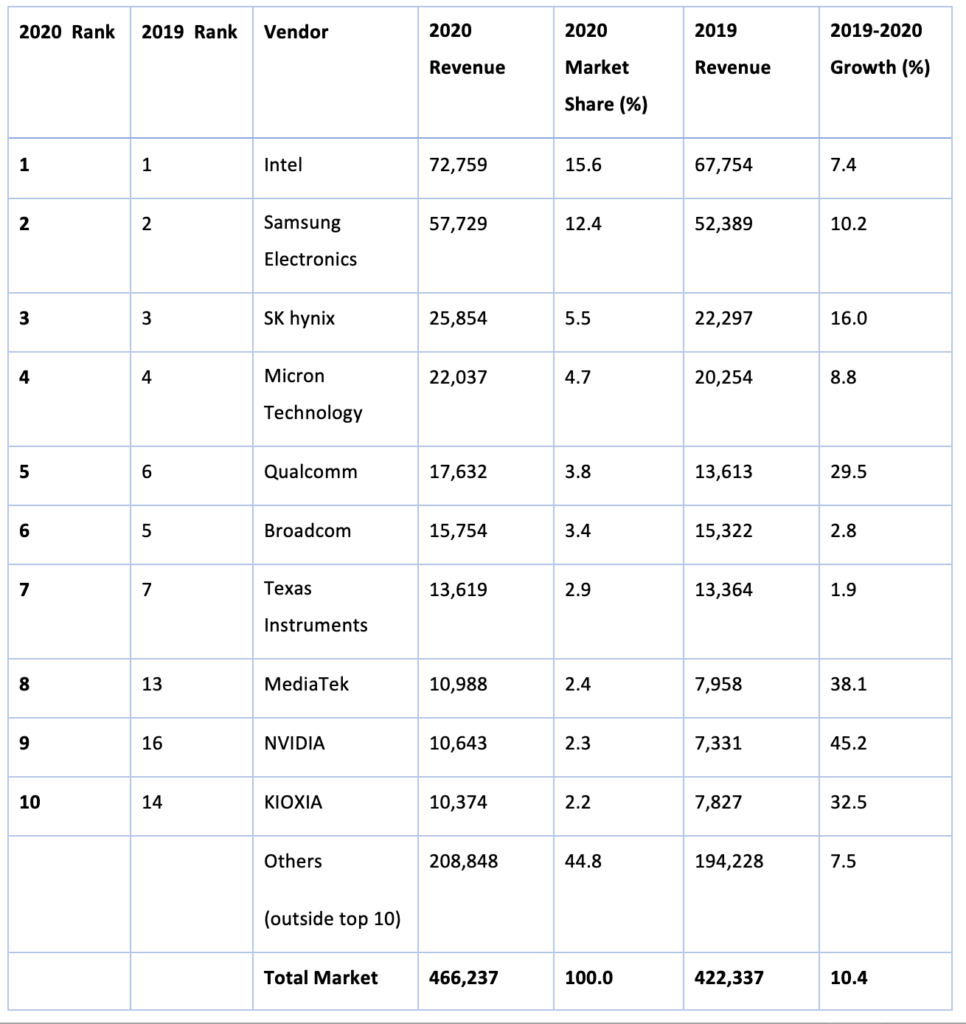
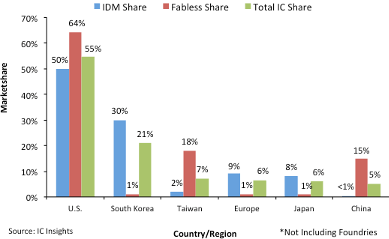
Four of the top 10 companies are fabless and account for 55 billion of the 466 billion totals for 2020 (Figure 4). Three of the four fabless companies are from the United States, which means six of the top 10 companies are US-based. So as IC Insights pointed out in a recent press release, The US owns a 55% share of the worldwide semiconductor market.
If this is the case, why is there a supply chain issue? As the data show, close to 64% of those chips are processed in a foundry, which means the majority of the chips are manufactured overseas, and then need to be shipped from overseas.
Looking at the data from SEMI’s 2021, Q1 World fab forecast, the trend shows that according to the past 15 years manufacturing capacity by region, growth outside of Japan, Europe, and the Americas has increased rapidly (Figure 5)
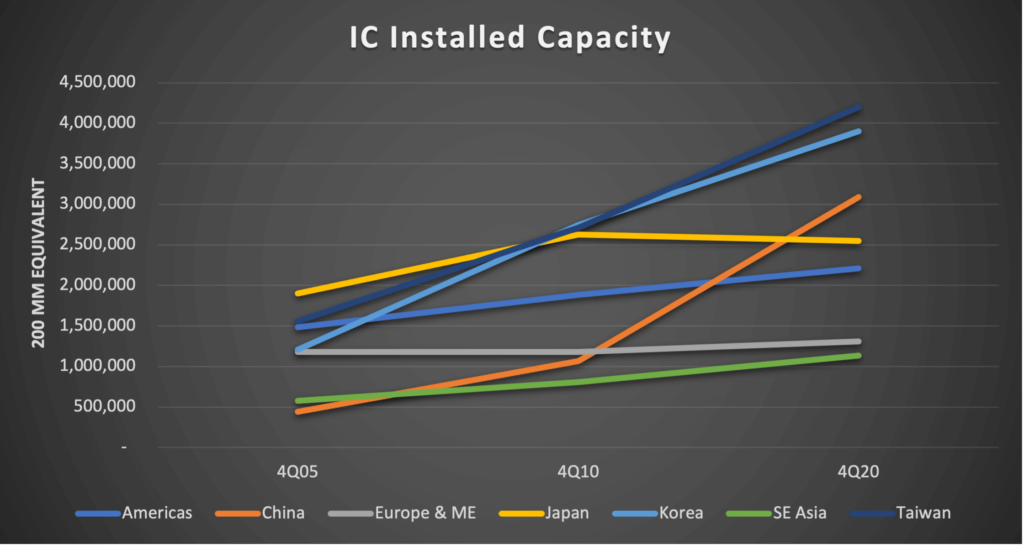
China’s growth has really boomed over the past five years outpacing all regions with 190% growth 2010-2020 compared to Taiwan’s 55% growth. While the US hasn’t been stagnant, wafer capacity has only grown at 17% over the past five years.
Why is the US Lagging and is Reshoring the Answer?
So, based upon this data. what is wrong? Six of the top 10 semiconductor companies by revenue are based in the US. Capacity has grown by 17%, albeit much less than Taiwan. Intel stumbled at 10 and then 7 nm, but according to Tom’s Hardware, Intel’s 10nm MPU outperforms a competitor’s 7nm MPU. R&D by Intel, and IBM are still at the cutting edge. The US has multiple microcontroller and analog manufacturers onshore that provide critical components in automotive and industrial. So, the US has significant manufacturing capabilities onshore already; however, they produce only half of the capacity that Taiwan does due to Taiwan’s strong foundry industry
What is more likely causing the tea kettle to boil over, is that while GlobalFoundries has made great strides in the past few years, a large majority of chips sold by US companies are still manufactured overseas, and on a just-in-time schedule. There is the additional concern that while Taiwan is still independent, there is enough saber-rattling to raise concern. To achieve change, the US will need to build a considerable legacy and leading-edge foundry capacity to meet the demand of US fabless chip companies. This is not a task that will be accomplished overnight. It will also have to learn to manufacture as economically as the overseas foundries. Morris Chang, the founder of TSMC was quoted recently saying: “Products made in the US would still be saddled with higher costs, even after federal and state governments had each chipped in with hefty investments and subsidies to make the Phoenix project possible.”
The semiconductor industry has been run on economics for most of its history. The company that can build high quality at the best price typically wins the business, which is one reason the electronics business is a worldwide business. Thus, convincing fabless companies to jump ship will likely be the most formidable challenge of reshoring the semiconductor industry. ~ Dean.