Another highlight of SEMICON West centered around 200mm fabs. The 200mm industry has thrived on used equipment. As 200mm memory fabs closed, a significant amount of that equipment made its way to existing or emerging logic lines. Most of these lines process chips that have linewidths, or technology nodes at 100nm or larger, if they fall into the 90-65nm technology node or below they are probably processed on 300mm wafers.
According to the discussion at the Bulls and Bears Session, the bulk of automotive chips are at 40nm or above. Only a few automotive chips are at the leading edge, and a significant portion of the below 40nm chips are at 28nm, so 200mm manufacturing is important to the automotive, and industrial industry. 200mm is also the sweet spot for RF, MEM’s Analog, Power Management ICs (PMIC), as well as the emerging silicon carbide market (SiC), for the upgrading of EV and the grid (Figure 1)
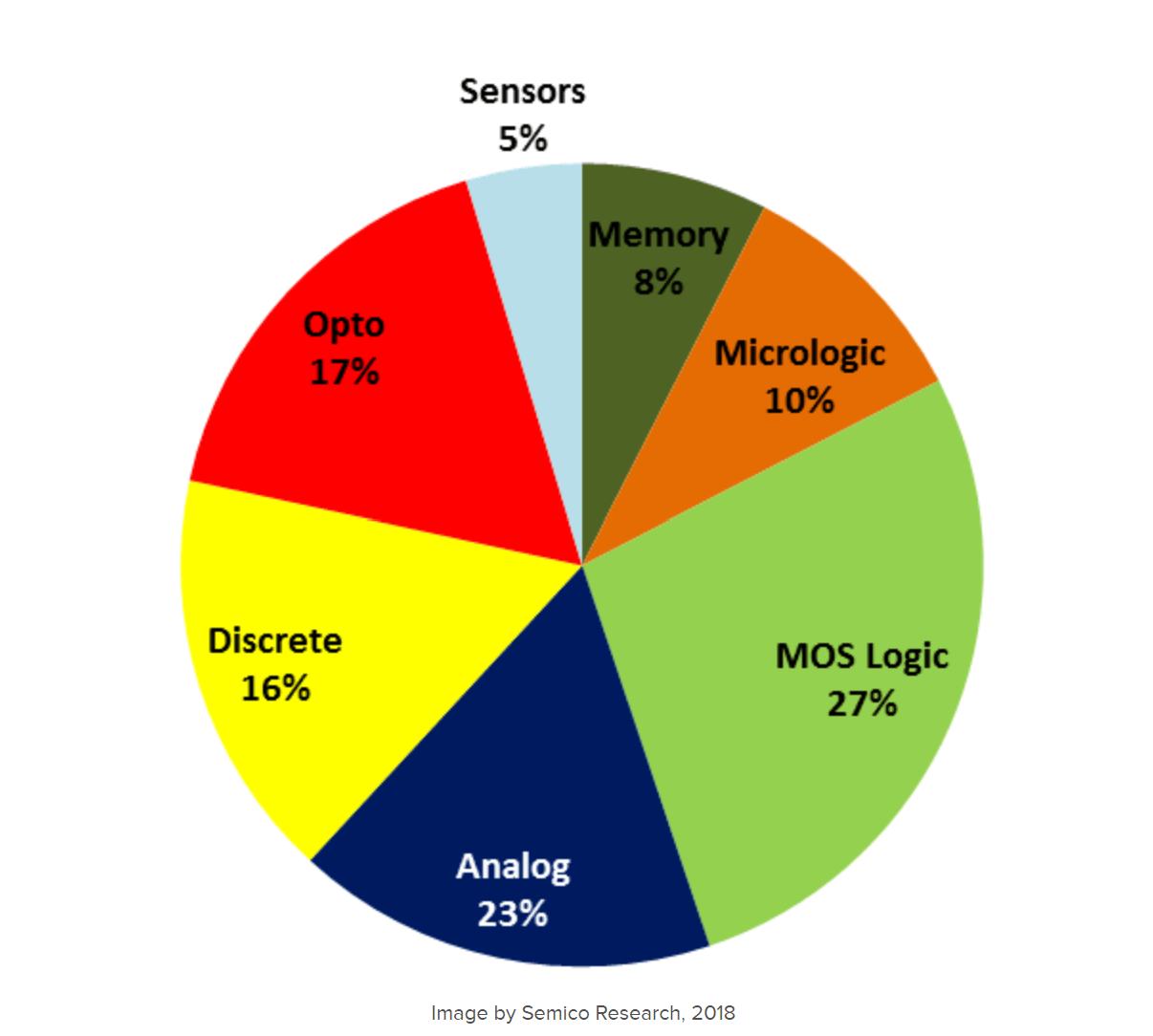
Most 200mm fabs are fully depreciated, which means everything is paid for and there are few if any costs associated with the building or equipment, other than the day-to-day cost of operations and chemicals needed to process the wafers. Thus, the cost to process the chips can be very inexpensive. The final price of the chip will depend upon demand. The Bulls and the Bears commented that a part that used to cost $5.00 was going for $80.00 during the height of the chip shortage. As old-timers in the industry know, when inventory becomes tight chip costs rise, when Inventory rises chip costs drop, sometimes below cost.
As a result of the chip shortage, and the need for 200mm capacity, a significant number of 200mm fabs are coming online. The March SEMI Fab report on 200mm fabs, estimates approximately 25 new 200mm fabs to come online between the start of 2020 and the end of 2024 (Figure 2). This appears to grow capacity from 5.8 million wafer starts per month (WSPM) to 6.8 million WSPM and means a capacity of about 40,000 WSPM per 200mm fab. The bulk of these fabs are going into China.
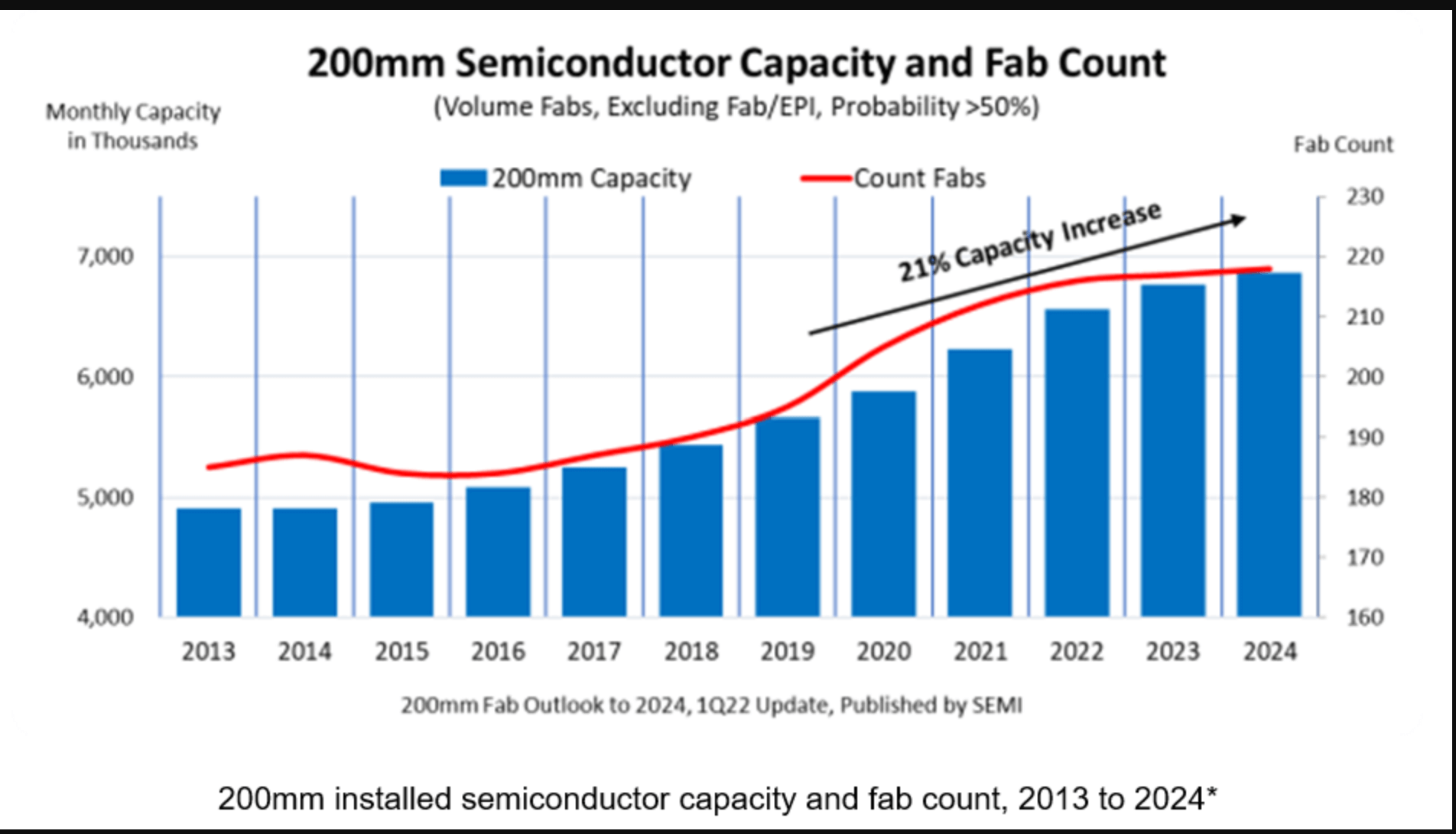
Over the past few years, the availability of 200mm process equipment has become extremely tight. In a discussion on the floor with Emerald Greig, Sr. Vice President of Business Development for PTW Group, she estimated that there were probably less than 100 200mm tools available on the market and that the condition of those tools was questionable. What this means is that the new 200mm fabs coming online will probably have to purchase new equipment to bring these fabs online. Why this is important is that with new equipment these fabs are probably costing around 2-3 billion dollars; roughly a billion for the building and the rest for equipment. If the fab was able to procure used equipment the cost would drop considerably, to about $500,000 or less for the equipment.
Since the deprecation of the equipment and building will impact the final cost of the chip, it’s safe to say that fabs producing chips on 200mm wafers using new equipment will need to be charging more for those chips than a legacy fab with no depreciation costs. This may have a significant impact on those new fabs, as the chip shortage eases, these fabs will likely need to reduce chip prices below costs. Typically, this means companies running at a loss, and if it goes on long enough getting acquired, or going out of business.
Since a significant number of these fabs are in China, it will be interesting to see if the Government bails them out, as it did for a while in the LED market space, or set the stage for acquisitions. When the LED market crashed, it completely blew up the LED manufacturing space, it made LEDs and lighting affordable, but moved most of the manufacturing to China. Thus, it is a real wait-and-see what happens to the 200mm chip manufacturing space as these fabs come online.
Editor’s Note: To gain more perspective on the role the secondary equipment market plays in the semiconductor industry, listen to this podcast interview with Bruce Kim, SurplusGLOBAL.