Semiconductor manufacturing involves many “chemicals of concern,” or compounds that are hazardous to human health and the environment. The hazardous compounds fall into several categories:
- Solvents—etchants, cleaners, and similar substances that are rinsed off the wafer
- Process chemicals—solids, liquids, or gases that undergo chemical reactions to form either sacrificial or permanent layers
- Solid materials—solders, polymers, and other materials that are part of the final product
Some of these compounds are hazardous during production but pose no danger once incorporated into a chip or circuit board. In this case, issues include limiting worker exposure and ensuring safe disposal or on-site recycling and reuse.
For hazardous substances that remain in electronic devices, proper e-waste handling is critical. A later blog post in this series will delve more deeply into e-waste.
Regulations and Restrictions
You are probably aware of the Restrictions on Hazardous Substances (RoHS) directive even if you aren’t familiar with the details. RoHS applies to certain elements and compounds used in electronics manufacturing and has been enforced for approximately 15 years. The original list of six restricted substances (heavy metals and flame retardants) has increased to ten with the addition of several phthalates used as plasticizers.
Replacing the restricted materials with safer alternatives is not simple. Sometimes the replacements come with unintended consequences. Other times no workable alternative exists. The 2011 update that replaced the original RoHS legislation states,
“Exemptions from the substitution requirement should be permitted if substitution is not possible from the scientific and technical point of view, taking specific account of the situation of SMEs [small and medium enterprises] or if the negative environmental, health and consumer safety impacts caused by substitution are likely to outweigh the environmental, health and consumer safety benefits of the substitution or the reliability of substitutes is not ensured.”
The statement above gives the industry a fair amount of leeway in deciding how to approach substitution. It opens the door to multiple exemptions, including those that might not be in the best interest of health and safety or the environment.
Solders are one example of the challenges of eliminating restricted materials. The initial replacements for Sn-Pb solders were alloys of Sn with additions of silver (Ag) and copper (Cu). Engineers struggled for years to improve the reliability of solder joints made from these SAC alloys.
SAC alloys melt at a higher temperature than Sn-Pb. That means that they require more time and energy to melt, which increases greenhouse gas emissions (GHG) during manufacturing. Does this drawback outweigh the benefits of removing Pb from solders? It might.
I am fascinated that the industry is now considering lower melting Pb-free alloys, including some that include bismuth (Bi) or indium (In). Back in the early 1990s, when a ban on Pb in solder in electronics was first being proposed, my PhD research focused on Sn-Bi and Sn-In.
RoHS and other regulations, however, extend far beyond solder alloys.
Understand the Hazards
Safety Data Sheets (SDS) spell out appropriate handling and disposal procedures for materials that are toxic, flammable, or otherwise hazardous. They often include ratings from the National Fire Protection Association regarding the level of health hazard, risks of fire and chemical instability, and other concerns.
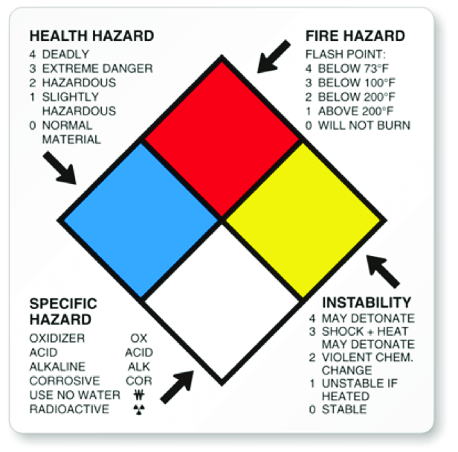
As an example, sulfuric acid has a health hazard rating of 3 out of 4 and an instability rating of 2. The SDS for sulfuric acid states that contact causes severe eye burns and skin damage. It warns against breathing fumes or vapors and requires workers to wear protective clothing. The SDS further advises against release into the environment including keeping the chemical away from drains, sewers, and waterways.
Many substances used in semiconductor manufacturing are much more hazardous than sulfuric acid. Some are endocrine disruptors, chemicals that mimic hormones and affect brain function and reproductive health. These chemicals are linked to multiple health problems, from infertility to neurological conditions.
Exposure to endocrine disruptors comes from many sources, including the food we eat, so eliminating them from the semiconductor supply chain will not solve the problem. But the polychlorinated biphenyls (PCBs, not to be confused with printed circuit boards) used in fluids and lubricants are endocrine disruptors.
Toward Safer Alternatives
Awareness of hazardous chemicals in your manufacturing process is the first step. The next step is mitigation. Here are some questions to consider:
- Is it possible to eliminate the hazardous chemical by replacing it with a safer one?
- If not, how can you reduce the quantity of the chemical in your process?
- Are workers being adequately protected from exposure?
- How is your facility handling waste disposal of the chemical?
The answers to these questions will point to possible solutions. These may involve training employees on safe handling or installing better filtration systems or monitoring devices. Or you may propose changes that take more time to implement, such as redesigning your process to accommodate a change in solvent type or concentration.
Changing a process requires investments of time and money. But there are payoffs in both the short and long run. You can:
- Protect your employees, customers, and the local community from health hazards
- Reduce hazardous waste disposal costs
- Differentiate your product in the marketplace
There are advantages to being proactive in considering what goes into your manufacturing process. The best way to reduce the risks associated with hazardous waste is to create less of it. By going beyond minimum compliance with regulations, your company help reduce the health and environmental impact of semiconductor manufacturing.