Here’s one thing the team at Rudolph has a firm grasp on: understanding that feature sizes of today’s wafer-level, 2.5D and 3D packaging technologies are changing the requirements for manufacturing tools in the back-end, and in many cases the back-end tools of today are starting to resemble the front-end tools of yesterday. Unfortunately, these tools are still expected to come at back-end tool prices. At IWLPC 2013, Rajiv Roy and Klaus Ruhmer sat down with me to chat about the work Rudolph is doing to develop tools for metrology, inspection and lithography processes for 2.5D and 3D packaging that help the industry have its proverbial cake and eat it too.
On the inspection and metrology side, explained Roy, the company has developed a system that combines metrology and inspection into one system (Figure 1).
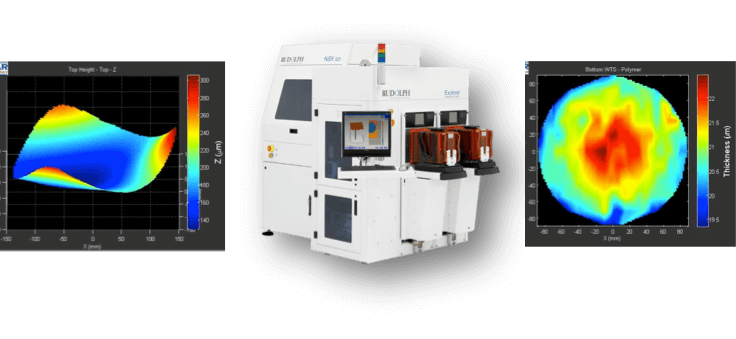
“The system is designed to address every aspect of TSV from the front to the back-end,” he said. “It’s the Swiss Army knife of metrology tools for TSV and Cu bumps, with metrology sensors that make it possible to measure RDL, height and polyimide thickness at the same time.” (Figure 2.) This is unusual because of the challenge of measuring a transparent film and a metal film in the same system. In the front-end, these tools are designed for either transparent only or metrology only.
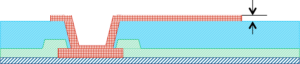
“Rudolph acquired Tamar Technology for the purpose of adding metrology capabilities to inspection,” noted Roy. “Rudolph’s NSX system combines IR-based sensors with white light interferometry sensors to perform two types of inspection: localized, such as for measuring via depth; and wafer level, for measuring thickness of various materials and nail protrusion height.”
I asked about void detection or total thickness variation for temporary bond/de-bond processes, and Roy told me Rudolph’s game plan is to enhance the tool with an IR camera for that application. I also asked about how Rudolph’s in-line tool compares with in-situ inspection for temporary bond/de-bond. “The reality is, macro-inspection and metrology help with yield ramp if you use it in line with your manufacturing processes. What we see is that an in-situ solution is not a great HVM scenario,” explained Roy. “A stand-alone system that can feed multiple process tools is a better alternative because any in-situ inspection takes away from real tool utilization and limits the flexibility of the tool.” A more flexible approach is to have a stand-alone tool, or several inspection tools in a line. This allows processes tools to function more efficiently. It’s ok to have a stack of wafers waiting for inspection, he noted. “
Ruhmer presented a paper that discusses how to meet 2.5D, 3D and fan-out back-end requirements (higher performance but not a higher price) by converging front-end, back-end and flat panel display manufacturing approaches. In some cases, such as with lithography for bumping, RDL or TSV to meet the fine pitch requirements that can’t be reached with non-litho patterning or proximity lithography, leveraging legacy front-end technology to the back end is one solution. He’s already noticing a shift from 1X systems (e.g. full field lithography) as these approaches are reaching their resolution (pitch), depth of focus and overlay limitations. Ruhmer said that 2X stepper technology is “the next logical step” to meet advanced packaging back-end requirements. Large depth of focus, continuous auto-focus from exposure shot to exposure shot, sub-micron overlay capability across the wafer and closed-loop integration of inspection and metrology are critical elements of back-end lithography (Figure 3). “In many ways, by adding some important capabilities, front-end lithography technology from 20 years ago is now getting a second wind in the backend,” noted Ruhmer.
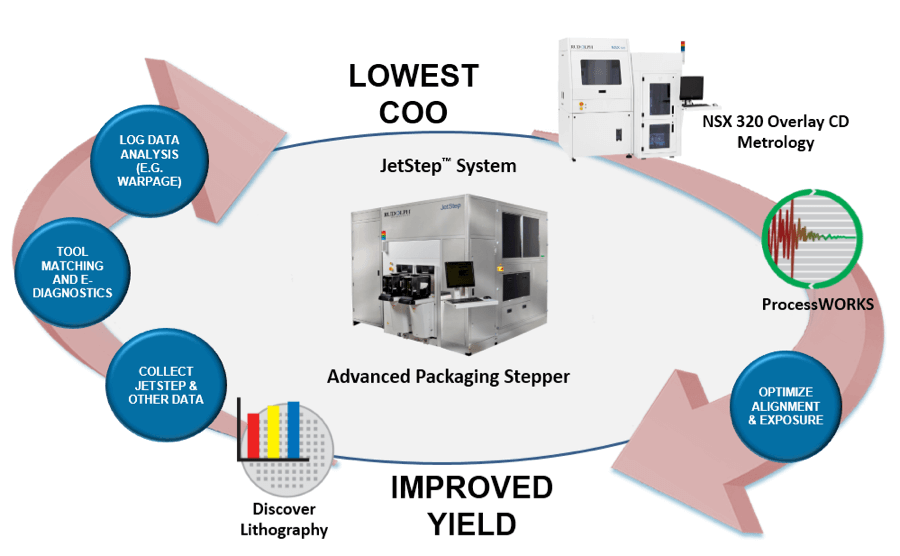
Additionally, leveraging flat panel technologies to build tools that allow us to reap the cost benefits of panelized packaging, such as for fan-out wafer level packages (FOWLP) or to enable low cost glass interposer technologies (which only offer a cost savings in panel format vs. wafer format.)
Ruhmer explained that in these cases, economies of scale enable lower cost per die, and therefore allow higher cost processes to become more affordable and suit back-end profit margins. Rudolph Technologies has combined the advantages of flat panel display with lithography stepper technology to further reduce the cost per die for panel fan-out processes. ~ F.v.T.