Those of you who have been in the advanced packaging world for 20 years or more may recall the tremendous challenges in replacing eutectic tin/lead (Sn/Pb) solder with lead-free alternatives. Pb is an excellent alloying element. Its low melting point and ductility are ideally suited for solder joints. Unfortunately, as we all know, Pb is highly toxic. It is more of a problem in our water supplies than our circuit boards, but it is easier to change the rules for the next generation of electronic products than to replace miles of plumbing lines.
Developing reliable SAC (tin/silver/copper) solder joints took years, but we did it. The Restriction of Hazardous Substances (RoHS) Directive didn’t give us a choice. Now the industry faces a new problem. How do we phase out PFAS chemicals in our manufacturing processes?
This is orders of magnitude more complex than dealing with solder because PFAS chemicals are everywhere, and many applications have no known substitutes. A recent study by the Semiconductor PFAS Consortium noted that “in some cases, the fundamental laws of chemistry and physics prevent the use of PFAS-free alternatives.” This statement suggests that not only are industry experts currently unaware of suitable alternatives, but such alternatives also cannot and will never exist.
SEMI President Ajit Manocha issued a dire warning in an interview on the 3D InCites podcast. “With PFAS, we have hit a brick wall,” he told Francoise von Trapp during SEMICON West. Other issues, like climate change and supply chain struggles, “will slow us down, but PFAS will shut us down.”
What does this mean, and what can we do about it?
Where are PFAS chemicals used?
PFAS chemicals appear throughout the semiconductor manufacturing process. They enable 193 mm and UV lithography, controlling surface tension and preventing pattern collapse. Fluorocarbon gases are required to etch silicon. The list goes on and on throughout nearly every process step.
The industry is aware of the tremendous challenge of finding workable substitutes. For some applications, research into PFAS-free alternatives has been ongoing for years. Despite these efforts, we are still many years away from solutions that can achieve the necessary performance. (Table 1)
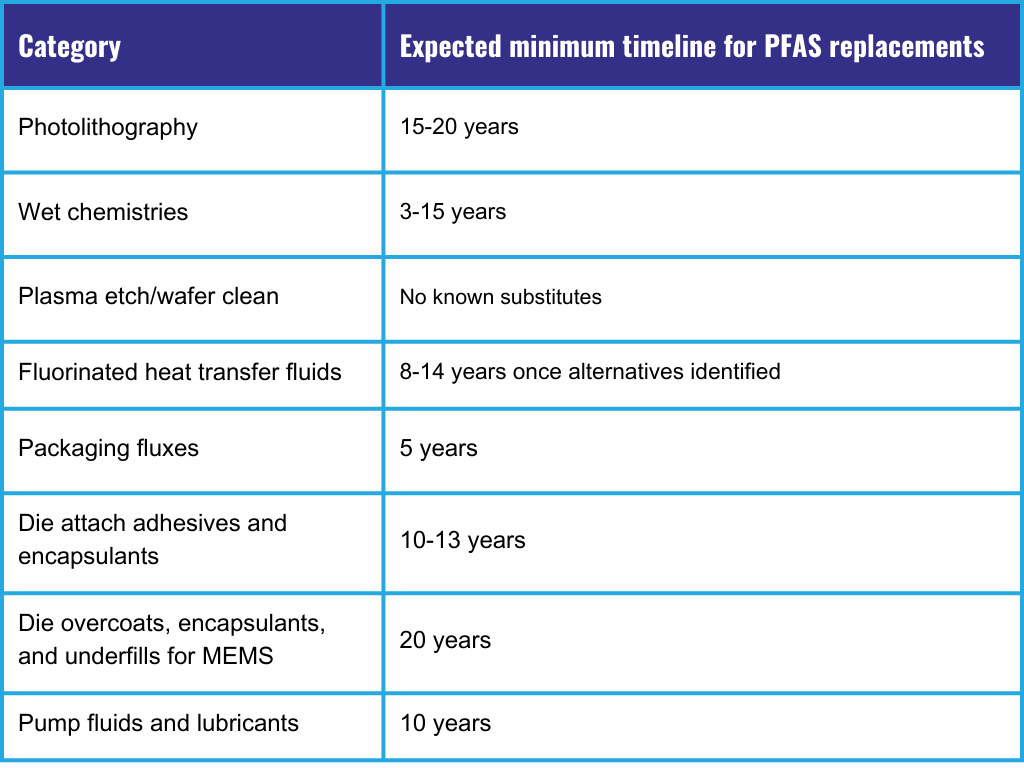
The Challenges of Replacing PFAS Chemicals
One challenge is identification. There are tens of thousands of PFAS chemicals, many of which appear in proprietary formulations. Suppliers are reluctant to release information beyond what they are legally required to disclose. Companies don’t even know all the sources of PFAS in their supply chains.
As noted above, even when alternative chemicals are identified, it takes years, even decades, to qualify them. They may or may not be able to achieve the same performance as PFAS chemicals. Any change in one process step causes a cascading effect on subsequent steps. Unacceptable yield drops are likely.
There is also the risk of introducing unwanted byproducts or that the alternative may be just as toxic as the chemical it is replacing. In the case of fluids and lubricants for equipment, replacing PFAS might cause increased failure rates, leaking other dangerous chemicals into the workplace. Since many potential replacements are untested, it is hard to predict what will happen.
PFAS Regulations
Regulations requiring the removal of all PFAS chemicals by 2025 or 2026 are well-intentioned. The sooner we can cease production of these dangerous chemicals, the better for public health. That makes sense in theory. For some sectors, it is doable. Some brands and product lines may disappear, but others will take their place. That is not the case for the semiconductor industry.
What would happen if we suddenly shut down all semiconductor fabs? It would halt commerce in multiple industries. Millions of people would lose their jobs. Production of everything from phones to vehicles to medical equipment would grind to a halt.
Demand for secondhand goods would skyrocket, along with prices, like what we saw with the chip shortage during the pandemic, only more so. Shutting down the semiconductor industry would wreak havoc worldwide.
Realistically, though, it will never get to that point. There will be exemptions and extensions for cases where PFAS chemicals are the only way to produce essential products. Semiconductors have become essential to society.
The semiconductor industry needs to work with regulators in governments around the world to explain the situation and gain the necessary extensions.
Parallels with Pb-free solders
In some ways, this feels a bit like RoHS. The amount of Pb in solders was minuscule compared to that in Pb-acid batteries. And it was only a potential public health hazard during e-waste processing. Regardless, the electronics industry had to phase out Sn-Pb solder.
Similarly, most PFAS chemicals used in semiconductor manufacturing do not end up in the final products. Since PFAS effluents haven’t been measured, it is hard to know whether the industry is responsible for releasing any of these chemicals into soil or water. But I think it’s safe to say that other industries bear far more responsibility for contaminating our water supplies.
Ironically, SAC solders melt at a higher temperature than eutectic Sn/Pb. That requires higher reflow temperatures and more energy consumption, which increases greenhouse gas emissions. Replacing PFAS-based lubricants with PFAS-free options would reduce equipment performance, likely increasing energy consumption. If the new lubricants don’t last as long, we will need to produce larger quantities.
My take? Keep the research going while exploring all the ramifications of any change and keep pressure on the regulators to ensure the industry doesn’t have to shut down.
Editor’s Note: If you missed the conversation between Ajit Manocha and Françoise von Trapp, find it here: