While the COVID-19 pandemic has continued to cause mass disruption to the global economy during the past year, one notable bright spot has been within the semiconductor industry, where fab spending in new process equipment reached a new record high of more than $100B according to SEMI. This spending growth was driven by both capacity expansion as well as investments to ramp up new process technologies into production. For EV Group, this has meant investments across the board in our wafer bonding, lithography, and metrology solutions, particularly those supporting 3D, heterogeneous integration and photonics manufacturing.
Besides seeing continued strong demand for our products, EVG also continued to see strong demand for our process development services, including those through our competence centers for heterogeneous integration and photonics. These innovation incubators enable us to work closely with partners and customers to help them develop new integration and device applications in these segments. Joint development agreements with Applied Materials and ASMPT involving wafer-to-wafer (W2W) and die-to-wafer (D2W) hybrid bonding, respectively, are just a few examples of our collaborative partnerships in heterogeneous integration. Our continued work with SCHOTT, Inkron, and others in developing high-volume manufacturing solutions for high refractive index waveguides, our work with ZKW in dynamic light projection technology leveraging micromirror MEMS type devices, and other partnerships, are helping to drive innovations in photonics for automotive, industrial and home entertainment applications.
Many industry analysts expect 2022 to be another strong year for semiconductor process equipment suppliers. We believe that heterogeneous integration will continue to be a strong driver for the industry due to the relentless pursuit of bandwidth scaling to support new industry megatrends such as high-performance computing (HPC) and artificial intelligence (AI). As many know, bandwidth scaling is closely tied to interconnect scaling. With tighter pitches between interconnects, more connections can be achieved within the same area on the device, which in turn means that more data can be transmitted. Higher bandwidth needs are driving newer packaging technologies. The transition from 2.5D to 3D SIC packaging, and from 3D SIC to 3D SoC packaging, can provide several orders of magnitude improvement in bandwidth. However, these new packaging technologies have tighter pitch requirements, which in turn drives the need for new and different hybrid bonding techniques.
W2W bonding processes are enabling new device fabrication concepts, such as memory-on-logic devices through the transfer of memory layers like NAND, DRAM, SRAM, or Flash from one wafer to another, as well as backside illuminated image sensors and other heterogeneous integration device applications. Improving overlay between wafers during W2W bonding enables the connection of different layers at earlier metal levels, which saves cost as well as increases device bandwidth and performance. For the production of the first generation of image sensors around a decade ago, W2W overlay in the range of 500nm to 1µm was sufficient. This has quickly scaled down with future device generations. Today, W2W overlay requirements for leading-edge applications today range from 500nm down to 100nm overlay pitches.
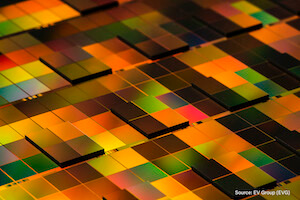
In D2W bonding, the dies, as well as the carrier/target wafers, typically have alignment patterns, which serve as fiducials for both patterning and alignment verification after full population. As hybrid bonding targets interconnect pitches from about 10µm down to 2µm in the future, the same scaling needs to happen for the placement accuracy as well as the metrology to control and yield the process. For future roadmaps targeting 2µm interconnect pitches, a factor of 10X improvement is required for placement accuracy and metrology precision (20nm for each).
While advancements in bandwidth and packaging are driving tighter specifications for hybrid bonding, EV Group is up to the challenge. At the center of our product roadmap is our emphasis on increasing product performance and maintaining flexibility in our product platforms to support our customers’ wide-ranging and ever-evolving requirements. In addition, our collaborations across the supply chain allow us to share data and learn from different areas of strength, which leads to better support for our customers in solving their critical manufacturing challenges.