Getting to zero carbon emissions will be a significant challenge for the semiconductor industry. With the industry expected to grow at a 7.1% CAGR through 2026 according to IC Insights, and units reaching 1.15 trillion in 2021 according to the SIA, reducing energy consumption and greenhouse gas (GHG) emissions will cause more than one vice president in charge of curtailing GHG emissions to lose sleep.
A recent article, by the Wall Street Journal, on how a Panasonic battery factory was able to get to zero emissions highlights the challenges in reducing one’s carbon footprint and GHG emissions.
Panasonic estimated that its emissions at this battery factory in Wuxi China were approximately 60,000 metric tons per year. Panasonic first installed solar panels on the roof of the building to generate clean energy, which cut emissions by 1250 metric tons. Only 58,000 metric tons to go!
The photo above shows the installed solar panels on the roofs of its Wuxi battery. (PHOTO: PANASONIC CORP. SOurce WSJ)
Next, according to the WSJ article, came the automation of processes using robotics. This reduced emissions by 2710 metric tons and had a side effect of reducing the number of employees by 38%. This would also reduce emissions by eliminating a significant number of commuting emissions. Innovative methods of operating the factories’ dust collectors, air compressors, and exhaust fans reduced emissions by 660 metric tonnes of CO2 each year. The implementation of LED lighting also helped in reducing emissions. However, when all the energy savings and renewable projects were implemented, the factory had only reduced emissions by 20%. This left 44,000 metric tons of CO2 emissions Panasonic had to address. To get to zero carbon emissions, Panasonic had to purchase renewable energy certificates, essentially purchasing renewable power, and carbon credits issued by projects such as planting trees, or protecting forests.
So, while we should congratulate Panasonic for getting a factory to zero, there is a twist in the plot that those going green need to pay attention to. While currently, the purchasing of green energy and carbon credits is fairly economical, the road to zero carbon emissions is still fairly new.
In my research studying companies’ proposed environmental reports, many companies have goals to get to 100% renewable by 2030, or zero emissions, as Panasonic has, but they are just beginning to implement these plans. As these plans start to become reality, will the installation of renewable power keep up, and how many trees can we plant, and forests can we preserve to create carbon offset credits?
As the author of the WSJ article points out, what Panasonic has realized is that it is very likely that the cost of renewable energy will rise as the demand exceeds the supply, and the same is likely for carbon credits. This especially concerns me for regions with a large electronics industry, such as Taiwan and Japan, that have limited land resources for solar, and limited ocean areas for wind. Getting to zero carbon emissions may be easy for companies that have a large bankroll, but more challenging for smaller companies as costs potentially rise. Other questions I have is how fast can we install renewable sources, can the electric grids support those sources, and what are the recycling plans for windmills, solar panels, and batteries? Currently, only 10% of solar panels are recycled in the United States, and battery recycling is in its infancy.
So, the question that most CEOs and sustainability directors need to be asking is how do we get the semiconductor industry to zero carbon emissions while the industry is expanding rapidly?
On the positive side companies, such as Intel, TSMC, ST microelectronics, ASE, have been taking sustainability seriously for some time. These companies’ sustainability reports go into a great deal of depth as to what they are doing to reduce GHG emissions and their renewable projects and could be used by companies starting sustainability programs as a template for how to proceed.
Over the last two years, SEMI has increased their focus on sustainability and have released their Semi sustainability initiative that we will hear more about at a SEMI Seminar on March 18th.
In December IMEC released its study of how the semiconductor process impacts GHG emissions. This enables both the equipment companies and the semiconductor manufacturers to target specific processes and chemistries and work to reduce those emissions. The study also highlights the need for a better electronics recycling program worldwide to keep electronic products out of landfills and to potentially recycle critical elements. IMEC is also working on developing chips for lower power consumption, which will help to reduce the power used by data centers.
At the Sustainable Semi Venture forum in September, EMD highlighted several new green chemicals that are being introduced to the process flow to reduce GHG emissions.
Last month SEMI and the venture selection committee picked the winners of the sustainability finalists. These companies will receive funding and advice. The three segments were materials, energy efficiency, and water technologies. One of the winners in energy efficiency, Verdigris, I’ve been following for a considerable time, and I am interested to see how its technology will be applied to the semiconductor industry.
TSMC has been very active in sustainability. I have blogged previously on its work with vendors to reduce power consumption in the sub-fab by idling abatement systems and pumps. Recently TSMC published work on developing an immersive cooling system for high-performance computing. The project proposes they would save 30% in energy and 50% in waste which are very significant numbers for today’s server farms.
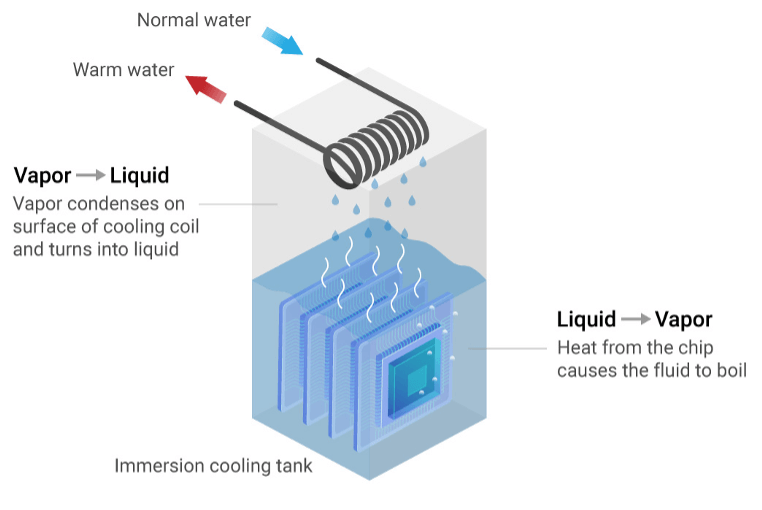
The new cooling process also can improve system performance by 10%, which would have the potential of reducing the number of servers required. This is a critical step as AI and edge compute power are expected to climb rapidly over the next few years. TSMC is encouraging staff to develop new energy and water reduction programs by providing time and resources for employees to explore studies that will improve sustainability.
Intel and other companies are looking at how to improve the performance and as a result the energy consumption of chips used in the server farms. Intel recently announced that the new XEON provides nearly a 2x performance in an end-to-end workflow. The improvement in CPU and accelerators, combined with better learning algorithms has the potential to help reduce the amount of energy needed to run HPC server farms, or localized edge compute (Figure 3).

Hopefully, with all parts of the supply chain pitching in, and new innovative solutions being explored, the industry can reduce the massive growth in power consumption that is predicted, help to minimize the increase in energy required to run compute in the future, and help to get us to zero.