My, what a fix the microelectronics industry has gotten itself into! Three crises happening all at the same time: One threatening the automotive industry, one our electronics supply chain, and the third the United States’ ability to remain competitive in the semiconductor space. There has been a bit written on these topics over the past few months, and hopefully, this reprise will be anything but boring. Unfortunately, the industry has created this mess over a long time period, and it will take a long time to sort it out. Sorting it out may also mean swallowing some bitter medicine, or higher costs if the United States plans on re-shoring the semiconductor industry that it off-shored in the 1990s.
Automotive Chip Shortage
Let’s start with the automotive chip shortage. I found a recent article in the Washington Post to be pretty amusing. Chip shortages don’t just happen unless there is a major earthquake in Taiwan, or a chip manufacturing plant burns down or loses power. None of this happened. Ok, we did lose power in Texas for two weeks, but the shortage was upon the industry before that.
This problem is a major screw-up by the automotive manufactures. Chip factories allocate production based upon orders. Auto companies stopped ordering chips. If I’m a smart foundry manager and my 28nm automotive orders dry up, I’m reallocating that production to another technology. It takes around 40-60 days from start to finish for a 28nm chip to get through the factory. The foundries, especially TSMC, are very good at switching to a different process technology quickly. And if you look at TSMC’s revenue from 28nm, where a large majority of automotive chips are manufactured, it was 11% in Q4 2020, down from 14% in Q2. And according to and Anandtech article, 16nm, which is another popular automotive node at TSMC, was at 13% of total revenue in Q4 2020, down from 18% in Q3. So somewhere along the line, someone had to have stopped ordering chips! Now the chip industry is to blame for someone in the automotive industry’s production planning screw up.
200mm Capacity is Constrained
Another challenge for automotive companies is that 200mm capacity is constrained, and most of the older chips are made on 200mm. Samsung and TSMC have developed automotive chip processes on 16nm, 8nm, and 7nm. Only the 16nm appears to be in production. Based on what I have been told by former co-workers, it takes a bit of time (years) for automakers to approve new technology nodes due to the testing needed to ensure reliability requirements for autos. To ensure that the automakers have the products they need, they must give chip manufacturers a solid plan for what they need, when they need it, and be ready to pay for it. This may mean paying upfront to ensure they have the capacity they need for the future. Too often, the industry is caught short by double orders, thereby exacerbating the shortage. And then, when the automakers have enough chips, they cancel orders, leaving chip manufactures with excess capacity and having to lay off staff they hired to meet the new demand.
This automotive chip shortage problem will be resolved like all shortage problems; once the automakers get their orders in and take their place in line. It may take a few quarters, as it looks like other industries stepped up to fill the void the automakers left when they stopped ordering. Hopefully, in the future, there will be better production planning from the automotive companies versus the age-old just-in-time manufacturing approach.
However, there is more to the story. When you dig deeper into the supply chain for automotive chips you soon find that the majority of the chips don’t come from Taiwan or China. Table 1 shows the top 10 automotive Chip manufacturers in 2018 held 62% market share, according to HIS.
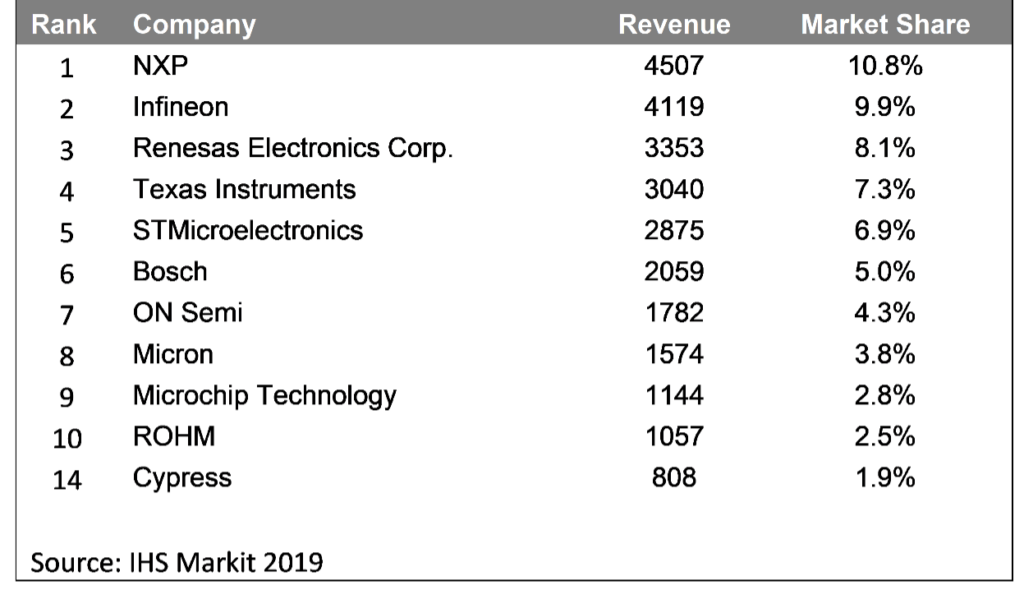
NXP, Texas Instruments (TI), On Semiconductor, Microchip, and Cypress Semiconductor all have manufacturing sites in the United States. With the exception of TI, all of these manufacturing facilities are 200mm. Thus, there are capacity constraints which in turn lead to the need for better partnering and ordering from the automotive companies. So that leaves 38% of a very fragmented market that might come from Taiwan. QUALCOMM and Xilinx are both involved in the automotive space and use TSMC as a foundry, but that doesn’t explain the shortage and the breakdown in the supply lines.
An Unexpected Early Rebound?
Another factor that possibly led to the shortage, is that according to IHS Markit the automotive market was expected to decline by 9.6% in 2020 and have a significant rebound in 2021 from about 38 billion in 2020 to 44 billion in 2021 according to their November 2020 forecast. Typically, based upon previous experience, when there is a forecast such as this, the semiconductor manufacturers begin to prepare themselves for a potential upsurge; however, if the orders don’t materialize, they then need to look elsewhere for revenue.
Who Dropped the Ball?
From my perspective in the automotive crisis, someone dropped the ball, and from the reports I’ve read, those someones are the automotive industry. It takes time to build the capacity for new chips that are needed for electric vehicles and autonomous vehicles. The automotive industry has been aware of this need for several years as they have been preparing for the launch of these new vehicles. Typically, chip manufactures have been working on chips for these vehicles years ahead of when they are needed and have been prepping for when they will win and receive the orders for the chips. It looks like this go-around the car makers forgot to let their partners know that they were ramping production.