It had been awhile since I heard from the folks at Alchimer about the progress of electrografting (eG), its “all wet” nanometric film deposition processes. For a while, it seemed like there were exciting things to report every few months, and then POOF – All went dark. So I was happy to find out that the company and its technology is alive, well and experiencing a re-bound after corporate and business model reorganization. At the European 3D TSV Summit, (Jan 22, 23 2013) I talked with Frederic Raynal, CTO and VP of engineering, and Vincent Mevellec, director of technology about the company’s new vitality and direction. (It was a reunion of sorts, since I had first met Raynal and Mevellec in 2010 when I visited the company headquarters in Massy, France.)
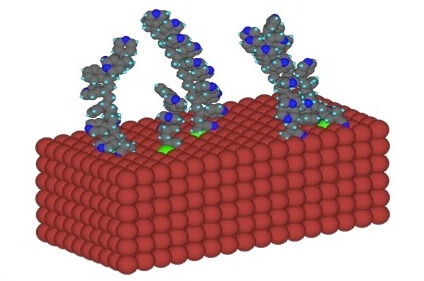
Just to recap, Alchimer’s core technology is nanometric film deposition based on surface chemistry formulations and processes for TSV copper isolation, barrier, (seed) and fill, as well as backside metallization. The technology is based on self-oriented layer growth of coatings that are initiated by reactions between precursor molecules and the substrate surface. eG can be performed in standard plating tools. The key difference between conventional deposition and Alchimer’s processes is that in eG, the films are “grown” rather than “deposited” on the target surface, as is the case with PVD and CVD. This allows for conformal coverage of any surface topography, while also allowing deposition in both vertical and horizontal directions (Figure 1). The company has introduced a product family based on this process, to complete TSV metallization including isolation, barrier, seed, , and fill steps.
The latest news shared by Raynal and Mevellec is twofold. The first, and most critical message is the new business model, under the guidance of Alchimer’s new CEO, Bruno Morel. Previously, the company operated under a standard licensing model. Alchimer performed evaluations for the customers, but the customers had to pay up-front to license the technology. Now, the model is royalty based, and the partnership is with the equipment manufacturers and the chemical suppliers. “We don’t impose anything on the manufacturer,” explained Raynal. “Alchimer’s assignee goes into the customer environment and works with them to set up the tools and qualify the process. When they go into production, the customer purchases the chemistry and equipment, and we receive royalties on the sale of the equipment and chemistry.”
Mevellec talked about advancements of the processes that allow for the elimination of the seed layer, with fill performed directly on the barrier layer. The R&D team is working to also eliminate the barrier step, and combine isolation and fill. But that’s down the road. Ready for production now are the isolation, barrier and fill processes (Figure 2).
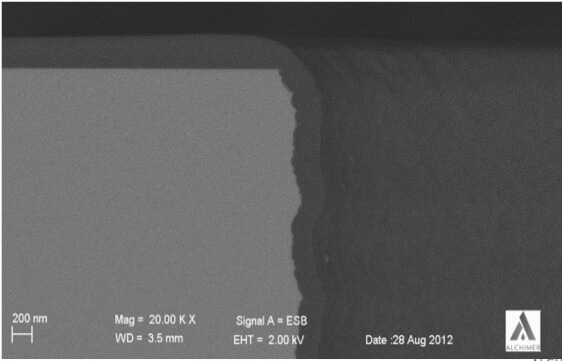
Mevellec also reported some promising statistics enabled by eG. He said they can achieve 100% coverage for thick copper seed layer, whereas PVD achieves less than 10%. Additionally, eG achieves 60% step coverage for the isolation layer, and 100% coverage for the barrier layer, while also reducing the overburden problem. While conventional processes are limited to a 10:1 aspect ratio, Alchimer’s processes have been demonstrated on up to 20:1 aspect ratio vias (Figure 3). The best number of all is the cost savings afforded by these processes. Mellevic says implementing eG results in a 30% decreased in cost of ownership (CoO) over conventional deposition processes, regardless of the dimension of the TSV.
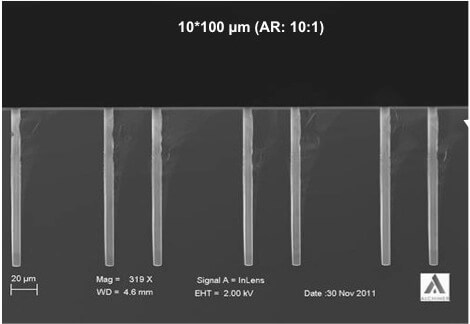
As we are on the brink of TSV commercialization, I’d say Alchimer picked the perfect time to resurface, particularly with the overall industry focus turning to optimizing processes to reduce cost of ownership. Raynal shared that the company is in qualification with three customers for TSV processes, and expect to move forward to pilot line production by mid-2013, with manufacturing at the end of 2013. There’s no doubt about it, things are looking up for Alchimer. ~F.v.T.