While working with a committee on evaluating multiple microelectronics companies for their efforts on sustainability an interesting question arose. Is a company being sustainable if it switches to renewables, but don’t reduce their energy footprint? In an industry where the semiconductor unit growth rate runs about 10% — TSMC builds a mega-Fab every 2-4 years, and there are new memory fabs nearly every year — is it possible to reduce energy consumption? The short answer is probably not, and the industry’s power requirements will continue to grow. But the long answer is that you can look at manufacturing methods to reduce the power consumed per unit or chip, and other ways to offset the amount of greenhouse gasses produced in the process.
Reducing Water Usage
Sustainability in the semiconductor industry wasn’t initiated with the Kyoto Protocols or the Paris Agreement. Semiconductor companies such as ST Microelectronics have been looking at how to reduce water usage and energy consumption since at least 1994. According to their 1998 corporate environmental report, “In 1997 alone, our investments in energy conservation and efficiency allowed the company to save $11M in electricity. In the same time frame, the saving for water was about $5M.”
Figure 1 shows ST’s focus on water and energy starting with a 1994 baseline.
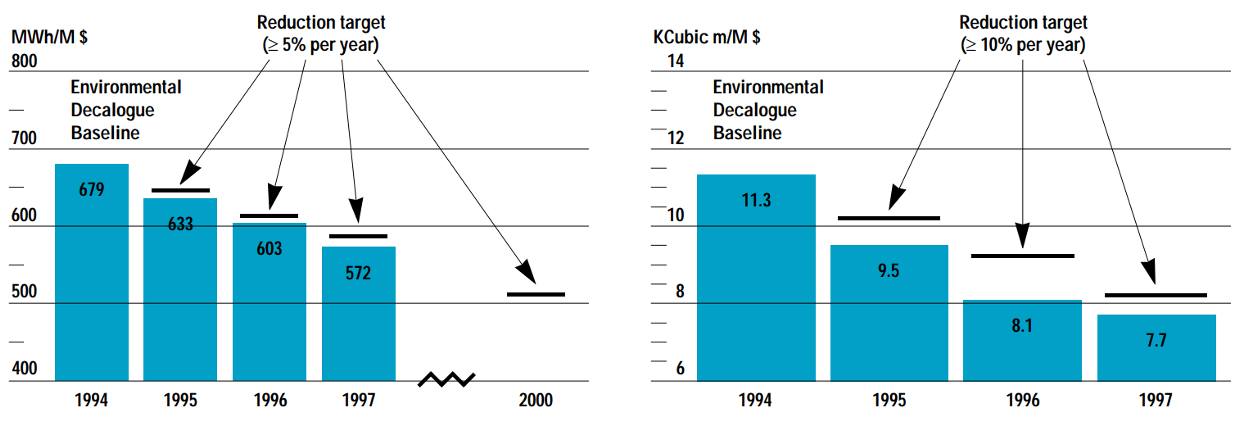
So as early as 1994 ST Microelectronics was focused on energy and water conservation. Intel was also an early adaptor of water conservation, in part due to its Rio Rancho facility and the challenges of sourcing water in the high desert, along with community action to get Intel to help preserve the local aquifer. Over the past two decades, Intel has been able to return about 80% of its water back to communities and has goals to restore 100% of its water use in the years to come.
Most semiconductor companies are looking to do a better job of reusing or recycling water, or returning wastewater to the environment after significant treatment to make sure the pH is similar to the local environment, contaminants such as fluorides or solids have been either removed. A facility I helped design back in the early ’80s was required to meet stringent requirements before the water was returned to the environment.
ASE Holding, one of the leading packaging companies with a significant amount of their operations in Taiwan, has been able to keep water intensity flat to slightly down over the past four years, which is impressive considering the increases in advanced packaging that has taken place during this time frame.
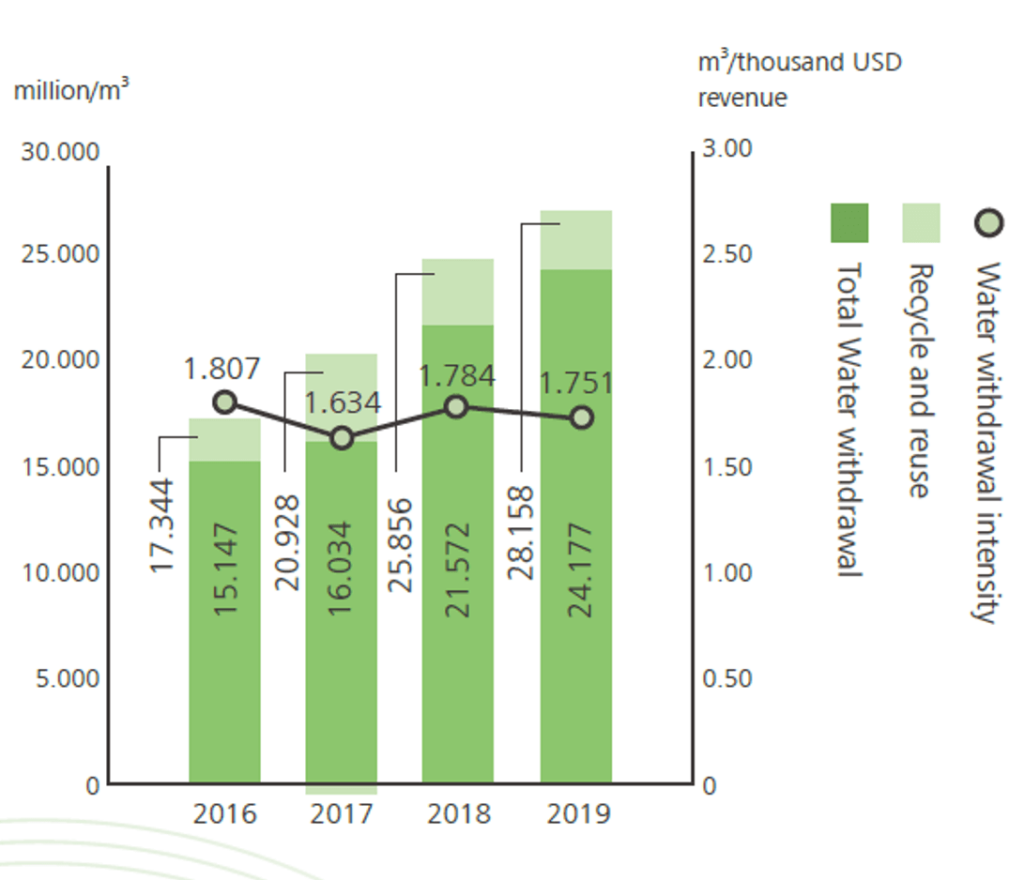
Source ASE 2019 CSR
What About Energy Conservation?
The conversation started with the question; Is a company being sustainable if it switches to renewables, but doesn’t reduce its energy footprint?
As with water, most semiconductor companies have been looking at how to conserve energy. Energy conservation and greenhouse gas reduction have been key corporate efforts for at least 15 years if not longer.
Most if not all semiconductor companies are on the renewable bandwagon. The table below shows how much of their energy supply comes from renewables. This is a good start. Most of the companies that were reviewed have plans to continue to increase their consumption of renewable energy, as it either becomes available or storage techniques improve such that the companies do not need to use non-renewable power sources at night for facilities that operate 24×7.

In looking at a company’s power conservation efforts, and power consumption, most have been able to save a considerable amount of energy through conservation, and keep power use relatively flat.
TI saved $34.4 million in utility costs since 2015 and total energy use went from 10.07 Million MMBtu to 10.21 Million MMBtu in 2019. Normalized energy per chip has been reduced to 0.38 in 2019, from 0.46 in 2015. The baseline was 1.0 in 2005.
ASE Holding measures normalized costs against thousand of US revenue. They have reduced their electricity intensity to 0.26 in 2019, a 0.57% reduction from 2018. However total energy consumption has risen from 2,227,268 MWh in 2015 to 3,588,896 MWh in 2019, according to their 2020 CSR. Much of this was due to their acquisition of SPIL
Intel has also increased energy use over the past 5 years. Increasing from 6.4 billion kWh to 9.6 billion kWh, along with an increase of CO2 emissions from 2.0 million metric tonnes, to 2.79 million metric tonnes. However, while the numbers show an increase in bulk CO2 emissions, the normalized production index has declined to 61 in 2019 from 100 in 2010, so a reduction of 39%
ST Microelectronics has reduced its CO2 emissions per unit of production by 29% over the same time period. ST Microelectronics has also reduced its net CO2 emissions by 57K tonnes over the past 5 years.
So, progress in reducing energy per unit produced or per value of revenue is taking place. In some cases, the CO2 being produced is also declining, in others, it is still increasing. As EUV emerges in the manufacturing space there will likely be a spike in energy consumption for companies such as Intel, Samsung, and TSMC. For companies like TI that are consolidating 150mm and 200mm fabs into 300mm fabs, the energy footprint will continue to consolidate. Meanwhile, the industry will need to continue its concerted effort towards a better sustainability footprint. ~ DF